The conversion of plastic waste into fuel is beneficial for the global economy and environment. Plastic conversion to fuel has the potential to create almost 40,000 jobs.
Advances in the Conversion of Ocean/MSW Waste Plastic to Fuels
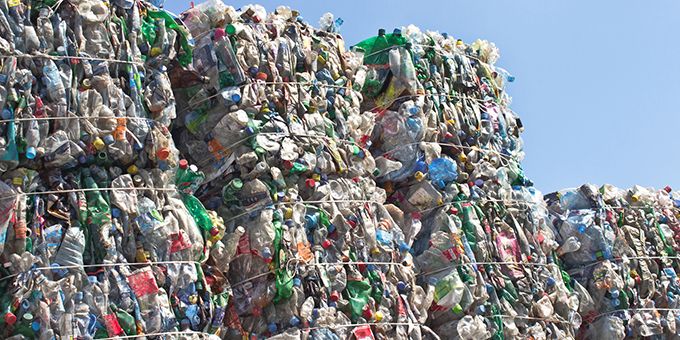
Dr. Raj Shah, Sharon Lin, Blerim Gashi | Koehler Instrument Company
Plastics are widely used throughout the world because of its cheap production cost, lightness, and durability [1]. Out of these plastics, the most used type is single-use plastics which are easily disposed of after each use. Without a doubt, there are many benefits to plastic, however, the use of plastic is detrimental to the environment. The durability of plastic, which may seem like a benefit is a disadvantage. This is because the durability of plastic makes it harder for plastic to naturally degrade [1]. Plastic contains polymers like polyethylene, polypropylene, polyvinyl chloride, polystyrene, and polyethylene terephthalate which gives plastic its durability [2]. Plastic also breaks down into microplastics which end up in the ocean and endanger the life of marine animals [1]. The Great Pacific Garbage Patch consists of at least 79 thousand tons of plastic, and it only continues to increase exponentially [3].
Plastic also affects the soil by changing the interactive forces between soil particles, therefore, affecting the health of plants and animals. Additionally, the absorption of micro-plastics from the soil, humans, and animals means that the micro-plastics accumulate in the food chain which affects the ecosystem [4]. To elaborate on its effect on the ecosystem, plastic may decrease the carrying capacity of the prey which would, in turn, lead to the extinction of the prey. This may also lead to the extinction of predators [5]. Therefore, plastic affects the balance of nature. One way to reduce this effect plastic has on the environment is to reduce the use of plastic. Although this may seem like a great idea, it is extremely difficult to stop using plastic altogether as it is an important material used every day. Therefore, different techniques were used to convert plastic into an energy source. This new energy source can be used to replace fossil fuels.
Biological degradation
Biodegradation is applicable for all types of plastics including polyethylene terephthalate, polyethylene, high-density polyethylene, low-density polyethylene, polyvinyl chloride, and many more [6]. Biological degradation is a heterogeneous process that occurs in stages [1]. First, plastic is introduced to microorganisms. The introduction of these microbes leads to the formation of microbial biofilms on the surface. Since microfilms are produced at a rapid rate, the plastic hydrophobicity decreases significantly. Hydrophobicity describes a property of plastic that repels water. Hydrophobicity can also affect the rate of degradation [6]. These microbes also secrete either endoenzymes or exoenzymes which contribute to the deterioration of plastic.
The plastic has now been broken down into oligomers, dimers, and monomers which will then be converted to CO2, H2O, or CH4. Abiotic and biotic factors affect the biodegradation of plastic [6]. Abiotic stages involve the chemical influence on plastic and can be affected by the temperature at which the process undergoes. The biotic stages involve the secretion of enzymes and can be affected by the microorganism and the type of enzyme secreted. Further research could be done on using abiotic stages before biotic stages to assist in degradation [7]. The type of microorganism used to biodegrade a plastic depends on the type of plastic. For instance, polyethylene can be biodegraded by using brevibacillus borstelensis or rhodococuus ruber [8]. Throughout the decades, a variety of research has been done on microorganisms to determine which microorganisms can degrade which type of plastic. Although biodegradation of plastic is a great method for converting waste to energy, biodegradation has not been used on a commercial scale due to its slow degradation rate.
Pyrolysis
Pyrolysis is a type of thermochemical conversion where oxygen is not needed to produce hydrocarbon fuels. Pyrolysis depends on many factors including temperature, heating rate, and the type of the reactor [1]. There are many types of pyrolysis such as flash pyrolysis, fast pyrolysis, rush pyrolysis, and intermediate pyrolysis. The yield depends on the type of compound pyrolysis is done on. For instance, pyrolysis of polystyrene produces liquid whereas compounds like polyethylene and polypropylene produce gas [1].
When thermal energy is applied to the pyrolysis process, plastic can be converted to gas and liquid oil. Plastic absorbs heat which causes the reaction to be thermal inducing [4]. Plastic was found to have a poor thermal conductivity which complicates pyrolysis. To address this issue, fluidized beds are used because of its heat and mass transfer properties. Due to this, the plastic macromolecules will be able to degrade [9]. Studies have shown that to increase the properties of the bio-oil, hydrogen is introduced during pyrolysis and a catalyst is used. This process is known as hydro-pyrolysis [10]. Hydro-pyrolysis is a relatively new subject and further research needs to be done to further understand it.
Liquefaction
Liquefaction is another type of thermochemical conversion where high pressure is applied and a catalyst is used to convert waste to bio-oil. High pressure is used because it prevents gasification of the liquid which increases the production of oil [1]. Liquefaction techniques are claimed to be costly which makes it harder to be commercialized.
Gasification
Gasification is another type of thermochemical conversion where organic molecules are converted to synthesis gas, which is a mixture of H2 and hydrocarbons. The process of gasification includes three reaction mechanisms. The plastic is first de-polymerized, which is similar to bio-degradation. The plastic is then decomposed through various techniques like dehydration, bond cleavage, and decarboxylation. After that, the reactive components are polymerized so it would not affect the production of oil [1]. After gasification occurs, Fischer-Tropsch synthesis is then implemented to produce low liquid yield and low carbon content [10].
De-polymerization Process
De-polymerization is the process of breaking down polymers into smaller pieces, like monomers. This process is often implemented in converting waste plastic to fuels as it reduces the energy content needed for conversion. Some methods of de-polymerization are catalytic cracking, thermal cracking, and reductive de-polymerization. Thermal cracking involves the use of high temperatures within the range of 500-800° C. This elevated temperature breaks the chemical bonds and forms smaller polymers. Catalytic cracking involves the use of a catalyst and produces hydrocarbons [11]. Reductive de-polymerization involves the use of a reducing agent to de-polymerize plastic waste. One example is polyethylene terephthalate which reacts with B(C6F5)3 and Et3SiH at approximately 20° C to produce BDM-Si and EG-Si. In this example, silane was used as the reducing agent, however, hydrogen, alcohol, and isopropanol could also act as the reducing agent [12].
Advanced oxidation process
There are many oxidation processes where oxidation is used to degrade the polymer. An example is Fenton oxidation where Fe2+ and H2O2 are used to oxidize a polymer. This produces CO2 which would be converted to acetic acid after photo-reduction [4]. Electrocatalytic oxidation uses metals that acts as the anode to produce a material that has the potential to have a strong oxidizing performance to degrade plastic [13]. This process can occur in direct or indirect oxidation. Direct oxidation involves attacking the polymer with O3 which produces OH. It was discovered that by using H2O2, the rate of degradation of plastic increases because of the increase in the formation of OH molecules [14]. Whereas indirect oxidation uses an electric field and a strong oxidizing agent, like OH, to degrade the polymer [13]. However, the need for an anode may be removed if an electroneutral compound, like NO3, is introduced [15].
Catalytic Oxidation
Catalytic cracking is the heating process of a mixture of catalysts and plastic waste to produce oil which can be converted to energy. This cracked oil is mostly made of aromatic hydrocarbons like benzene and toluene [4]. Photocatalytic conversion of plastic occurs in two steps. The first step degrades plastic into CO2 through C-C bond cleavage. The second step is to convert CO2 into C2 to produce fuel [16].
Examples of Utilization of Conversion Techniques
In a study done in Bangladesh, pyrolysis was used to convert waste plastic into energy. Low-density polyethylene and polypropylene underwent batch pyrolysis. At 270° C, the plastics vaporized and were condensed. At 400° C, the product was fuel oil, and the total yield was approximately 55% of the original amount of plastic.
In another study, high-density polyethylene, polypropylene, and polystyrene were mixed with lubricant oil. This mixture underwent pyrolysis at 450° C and the product had similar properties to diesel oil. This means that the co-pyrolysis of these plastics and the lubricant oil can replace the need for diesel.
In another study done with the use of Bangladesh waste, the high-density polyethylene was pyrolyzed at around 400° C for approximately 3 hours to produce hydrocarbons. The product was found to have similar properties as petroleum diesel.
In each of these studies, before the plastic could undergo pyrolysis, the plastic waste was broken down into smaller pieces. After that, plastic underwent pyrolysis at 400° C and after 20 minutes, the reaction started vaporizing. To achieve the product, the vapor had to be condensed. Although there were many methods of condensation, water was used as it was the most efficient and cheapest option. After the gas was condensed and produced oil, the gravity method was implemented to remove the oil from the water. The fuel oil then underwent the viscosity, density, water content, bomb calorimeter, flammability, and flash point test to measure its properties. These tests were done according to the ASTM method [17].
Conclusion
There are many conversion techniques to convert plastic to energy. These techniques include biodegradation, pyrolysis, liquefaction, and oxidation. As research on these techniques continue to provide insight, advances in degrading plastic could lead to the commercialization of converting plastic to energy.
About the authors
Dr. Raj Shah is a Director at Koehler Instrument Company in New York, where he has worked for the last 25 years. He is an elected Fellow by his peers at NLGI, STLE, InstMC, RSC, CMI, AIC, IChemE, Institute of Physics and the Energy Institute.
A Ph.D in Chemical Engineering from The Penn State University
( https://www.che.psu.edu/news-archive/2018/alumni-spotlight-raj-shah.aspx)
a deemed esteemed engineer title holder from Tau beta Pi ( world’s largest engineering society ) , and a Fellow from The Chartered Management Institute, London, Raj just became one of the first folks in the USA to be qualified as a Chartered Petroleum Engineer with the Energy Institute. An adjunct professor at the Dept. of Material Science and Chemical Engineering at State University of New York, Stony Brook, Raj has over 450 publications and has been active in the alternative energy industry for 3 decades.
More information on Raj can be found here:
Ms. Sharon Lin and Mr. Blerim Gashi are students of Chemical engineering at SUNY, Stony Brook University, where Dr. Shah is the chairman on the external advisory board of directors, and both Blerim and Sharon are also currently an integral part of the thriving internship program at Koehler Instrument Company, in Long Island, NY.
References
[1] Nanda, & Berruti, F. (2020). Thermochemical conversion of plastic waste to fuels: a review. Environmental Chemistry Letters, 19(1), 123–148. https://doi.org/10.1007/s10311-020-01094-7
[2] Jiao, Zheng, K., Hu, Z., Zhu, S., Sun, Y., & Xie, Y. (2021). Conversion of Waste Plastics into Value-Added Carbonaceous Fuels under Mild Conditions. Advanced Materials (Weinheim), e2005192–e2005192. https://doi.org/10.1002/adma.202005192
[3] Lebreton, Slat, B., Ferrari, F., Sainte-Rose, B., Aitken, J., Marthouse, R., Hajbane, S., Cunsolo, S., Schwarz, A., Levivier, A., Noble, K., Debeljak, P., Maral, H., Schoeneich-Argent, R., Brambini, R., & Reisser, J. (2018). Evidence that the Great Pacific Garbage Patch is rapidly accumulating plastic. Scientific Reports, 8(1), 4666–15. https://doi.org/10.1038/s41598-018-22939-w
[4] Li, Liu, H., Cheng, Z., Yan, B., Chen, G., & Wang, S. (2022). Conversion of plastic waste into fuels: A critical review. Journal of Hazardous Materials, 424, 127460–127460. https://doi.org/10.1016/j.jhazmat.2021.127460
[5] Wang, Sentis, A., Tüzün, N., & Stoks, R. (2021). Thermal evolution ameliorates the long‐term plastic effects of warming, temperature fluctuations and heat waves on predator–prey interaction strength. Functional Ecology, 35(7), 1538–1549. https://doi.org/10.1111/1365-2435.13810
[6] A, K, A., M, H., K, S., & G, D. (2020). Review on plastic wastes in marine environment – Biodegradation and biotechnological solutions. Marine Pollution Bulletin, 150, 110733–110733. https://doi.org/10.1016/j.marpolbul.2019.110733
[7] Qin, Mou, J., Chao, C. Y. H., Chopra, S. S., Daoud, W., Leu, S., Ning, Z., Tso, C. Y., Chan, C. K., Tang, S., Hathi, Z. J., Haque, M. A., Wang, X., & Lin, C. S. K. (2021). Biotechnology of Plastic Waste Degradation, Recycling, and Valorization: Current Advances and Future Perspectives. ChemSusChem, 14(19), 4103–4114. https://doi.org/10.1002/cssc.202100752
[8] Bahl, Dolma, J., Jyot Singh, J., & Sehgal, S. (2021). Biodegradation of plastics: A state of the art review. Materials Today : Proceedings, 39, 31–34. https://doi.org/10.1016/j.matpr.2020.06.096
[9] Kaminsky. (1995). Chemical recycling of mixed plastics of pyrolysis. Advances in Polymer Technology, 14(4), 337–344. https://doi.org/10.1002/adv.1995.060140407
[10] Perkins, Batalha, N., Kumar, A., Bhaskar, T., & Konarova, M. (2019). Recent advances in liquefaction technologies for production of liquid hydrocarbon fuels from biomass and carbonaceous wastes. Renewable & Sustainable Energy Reviews, 115, 109400–. https://doi.org/10.1016/j.rser.2019.109400
[11] Wołosiewicz-Głąb, Pięta, P., Sas, S., & Grabowski, Ł. (2017). Plastic waste depolymerization as a source of energetic heating oils. E3S Web of Conferences, 14, 2044–. https://doi.org/10.1051/e3sconf/20171402044
[12] Fernandes. (2021). Reductive depolymerization as an efficient methodology for the conversion of plastic waste into value-added compounds. Green Chemistry : an International Journal and Green Chemistry Resource : GC, 23(19), 7330–7360. https://doi.org/10.1039/D1GC01634B
[13] Liu, S., Wang, J., Li, R., Tian, Y., Teng, J., Li, Z., & Zhu, X. (2021). Study on electrocatalytic oxidation technology of domestic sewage. IOP Conference Series: Earth and Environmental Science, 791(1), 012198. https://doi.org/10.1088/1755-1315/791/1/012198
[14] Mohan, Mamane, H., Avisar, D., Gozlan, I., Kaplan, A., & Dayalan, G. (2019). Treatment of Diethyl Phthalate Leached from Plastic Products in Municipal Solid Waste Using an Ozone-Based Advanced Oxidation Process. Materials, 12(24), 4119–. https://doi.org/10.3390/ma12244119
[15] Kakegawa, H., Kashimura, S., Ishifune, M., Murai, Y., Tamai, Y., Isoko, T., Sasaki, Y., & Hirose, R. (2005). Indirect surface oxidation of milled carbon fiber and its application to carbon fiber reinforced plastics. TANSO, 2005(219), 246–248. https://doi.org/10.7209/tanso.2005.246
[16] Jiao, Zheng, K., Chen, Q., Li, X., Li, Y., Shao, W., Xu, J., Zhu, J., Pan, Y., Sun, Y., & Xie, Y. (2020). Photocatalytic Conversion of Waste Plastics into C2 Fuels under Simulated Natural Environment Conditions. Angewandte Chemie (International Ed.), 59(36), 15497–15501. https://doi.org/10.1002/anie.201915766
[17] Jannat, Akter, S., & Ehsan, M. (2019). Conversion of waste polypropylene plastic into fuel. AIP Conference Proceedings, 2121(1). https://doi.org/10.1063/1.5115946
[18] Christopher, F.J., Kumar, P.S., Vo, DV.N. et al. Methods for chemical conversion of plastic wastes into fuels and chemicals. A review. Environ Chem Lett (2021). https://doi.org/10.1007/s10311-021-01329-1
The content & opinions in this article are the author’s and do not necessarily represent the views of AltEnergyMag
Comments (0)
This post does not have any comments. Be the first to leave a comment below.
Featured Product
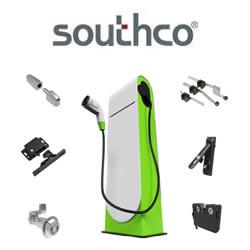